Cutting Slots In Mdf
- Cutting Slots In Composite Decking
- Cutting Slots In Mdf Boards
- Cutting Slots In Mdf Sheets
- Cutting Slots In Mdf Board
The biscuit jointer cuts a 4mm groove (ideal for 4mm MDF). The saw cuts about 2.8mm (3.2mm if on my table saw), so if a wider groove is needed I run a piece of 2in electrician's tape along the fence, make a cut, remove the tape (wiping any sticky bits with lighter fuel) and make a second cut. Next, we cut slots on the edges of each of the boards. One inch from the edge, we marked off a slot of 3/4 inch wide and half the length deep of the size of the board (12 inches deep). We used a circular saw to make the cuts from the bottom edge of the boards. The cuts that needed to be made on a right angle, we used a Dremel. In addition, if you are cutting wood that is more than 0.5 inches, you will require a bigger tool. Cut-off wheels are known to be small but straight bits, on the other hand, are the best when cutting wood. When you purchase a Dremel rotary tool, you might get a cutting kit that offers you a variety of attachments to use. Using the router and a slot-cutting bit to cut the slot for the T-molding. Using the router and a slot-cutting bit to cut the slot for the T-molding.
Question
I am building shaker doors with a 15 degree bevel using a bit set that cuts a 1/4' slot. The trouble I'm having is finding true 1/4' ply. Everything seems to be about 3/16'. This must be a common problem, but no one seems to have any solutions. Does anyone have any suggestions?
Forum Responses
(Cabinetmaking Forum)
From contributor R:
Here is a common fix: take your slot cutter to your sharpener and have them grind it to the right width.
From contributor L:
There are a couple of ways to get around this. If it is paint grade then use MDF that is 1/2' thick and run it through your panel shaper and put the panels in backwards. If it is a stain grade door then use 3/8' to 1/2' ply and cut a 1/4' tongue on it so the rabbet is on the rear side. This way you don't need to have your cutter re-sized and the need for you to do a re-setup of your machine. I suppose you could run your plywood through the panel cutter if it is a baltic birch or other similar multi ply plywood.
From contributor W:
Most suppliers carry veneer faced MDF that is 1/4' thick.
From contributor L:
To contributor W: I find that 1/4' MDF barely fits into my 1/4' slots as it is. Put two faces of veneer on them and I can't see it fitting.
From contributor H:
1/4' veneer with MDF core is 1/4' thick.
From contributor B:
We've got straight bits that are plywood bits; they run a little closer than standard 1/4, 1/2, 3/4 and etc. Instead of plywood, I would suggest looking for bits. You might as well get used to it because plywood seems to get smaller and sloppier all the time.
From contributor L:
I didn't know that it would be 1/4' finished. I figured they took standard 1/4' MDF and applied the veneer to it making it slightly thicker than 0.250'.

I have 1/4' maple veneered MDF from previous jobs and it also is roughly 3/16'. I guess it can all vary.
From contributor D:
You could try one of Amana's new adjustable slot cutters so you could adjust the slot on each run to fit the panel that you have on hand. I saw them advertised for about $100 bucks in woodshop news
From contributor S:
I assume this is stain grade. I worked for a high end shop that puts the 3/16' thick panel in the 1/4 slot and pin tack the panel into the groove from the back. I think this is totally acceptable procedure. Fpr paint grade I take a 3/8' panel and 'scoop' out the back to leave a 1/4' tongue.
From contributor M:
1/4 plywood will measure anywhere from .202 to .210. Most industrial cutters are set to cut your slot at these dimensions. I would look at getting a set of cutters with inserts and end any future problems
From contributor F:
I run my flat panel door parts on a shaper. Depending on what type of panel material I have needed or which of my suppliers have had the material, I too have had to accept the fact that the panel thicknesses are all over the map.
The way I have dealt with it is to buy two additional 2 piece sets of panel groover and tongue cutters for my Freeborn cope and pattern door knives. I can now run panel grooves and matching tongues at 1/4', 5 mm and 5.5 mm.
I personally like my panels to fit the groove snugly to eliminate panel rattle and I don’t want any brad holes in the back of the panel. So, if the panel stock doesn’t fit one of my three choices for groove width properly, I set the groover that is just a little smaller (thinner) than the panel thickness on the spindle and shim it to run eccentrically to machine the correct groove width.
This of course necessitates shimming the tongue cutters so that the tongue fits properly as well.
I haven’t tried shimming router bits that are made for doors, but I just looked at some in a catalog and I think it would be possible to shim the groover to run eccentrically and also shim the tongue cutter for the right fit.
From contributor T:
To the original questioner: Contributor W is right on about the 2 sided MDF veneer. The stuff that we use is .242 thick so you can just run your normal slot cutter if you want to run regular 1/4' (somewhere around 3/16') then do as others have suggested and use a 5.5 mm slot.
From contributor W:
1/4' seems too flimsy to me and I have an aversion to MDF in cabinets so I use 3/8' ply. I cut the groove on a shaper with a 1/4' slot cutter with the cutter height adjusted so that by running the piece through twice (each side up) I get a snug fit. Two problems I encountered that I've solved are: I was tormented by chip-out - solution: I make a 1/16' or so scoring cut by climb-cutting. Then cut the full depth the normal way.
For painted doors, any gap sticks out like a sore thumb - it's usually uneven and nasty looking no matter how well the panel to frame fit is. I solve this by first running a chisel brush around the gap with primer on it. I pack it in so it seals the gap, then spray the primer. Sometimes I'll have to repeat with one of the two top coats.
From contributor A:
We go about it from the panel thickness. We use the Freud adjustable dado set to dial in the thickness of the panel and then it’s off to the router table for the profiles wanted.
Would you like to add information to this article?
Interested in writing or submitting an article?
Have a question about this article?
Have you reviewed the related Knowledge Base areas below?
Would you like to add information to this article? ... Click Here
If you have a question regarding a Knowledge Base article, your best chance at uncovering an answer is to search the entire Knowledge Base for related articles or to post your question at the appropriate WOODWEB Forum. Before posting your message, be sure to review our Forum Guidelines.
Questions entered in the Knowledge Base Article comment form will not generate responses! A list of WOODWEB Forums can be found at WOODWEB's Site Map.
When you post your question at the Forum, be sure to include references to the Knowledge Base article that inspired your question. The more information you provide with your question, the better your chances are of receiving responses.
Return to beginning of article.
Refer a Friend Read This Important Information Site Map Privacy Policy Site User Agreement Letters, questions or comments?E-Mail us and let us know what you think. Be sure to review our Frequently Asked Questions page. Contact us to discuss advertising or to report problems with this site. To report a problem, send an e-mail to our Webmaster Copyright © 1996-2020 - WOODWEB ® Inc. All rights reserved. No part of this publication may be reproduced in any manner without permission of the Editor. Review WOODWEB's Copyright Policy. The editors, writers, and staff at WOODWEB try to promote safe practices. What is safe for one woodworker under certain conditions may not be safe for others in different circumstances. Readers should undertake the use of materials and methods discussed at WOODWEB after considerate evaluation, and at their own risk. WOODWEB, Inc. 335 Bedell Road Montrose, PA 18801 Contact WOODWEB |
This article is from Issue 21 of Woodcraft Magazine.
Because biscuit joints are easy to mark out and quick to cut, using one almost seems like cheating. In truth, biscuits may not be as strong as some traditional types of joinery and may not be suitable for heavy-duty loads, but they’re perfect for plenty of projects. Woodworkers and carpenters have been employing biscuits to successfully solve all sorts of assembly and alignment problems for over two decades. The easiest way to appreciate their versatility and strengths is by putting them to use.
The safest way to cut biscuit slots is with a biscuit joiner. This tool is designed to do nothing but plunge-cut arc-shaped slots. (Unlike the router/biscuit-cutting bit combo, the biscuit joiner’s cutter retracts inside the tool as you pull it away from your work.) From there, a flat, football-shaped piece of compressed wood, called a biscuit, fits into a pair of matching slots.
What makes biscuits better than dowels? The size and shape of the slot. The oversized slot lets the biscuit move slightly, enabling you to tweak parts into perfect alignment. However, once glued, the biscuits swell and lock the parts in place.
You can master basic biscuit joiner use in five minutes, but you will continue to learn new tricks with each project. Following are some common joints that you can practice making to familiarize yourself with a new tool or get better reacquainted with your old workhorse.
begin with the two slot test
A biscuit joiner should cut a slot slightly deeper than half the width of the biscuit you’re trying to fit. This space provides some wiggle room, but still ensures that about half remains on each side of the joint. Here’s how to check your joiner’s depth setting. First, make a test slot. Next, stick in a biscuit and mark a pencil line where the biscuit touches the wood, as shown in Photo 1. Now flip the biscuit and mark a second line. Adjust the depth-setting dial on your tool so that overlap is about 1/8', as shown in Photo 2.
THE face-TO-edge BISCUIT JOINT

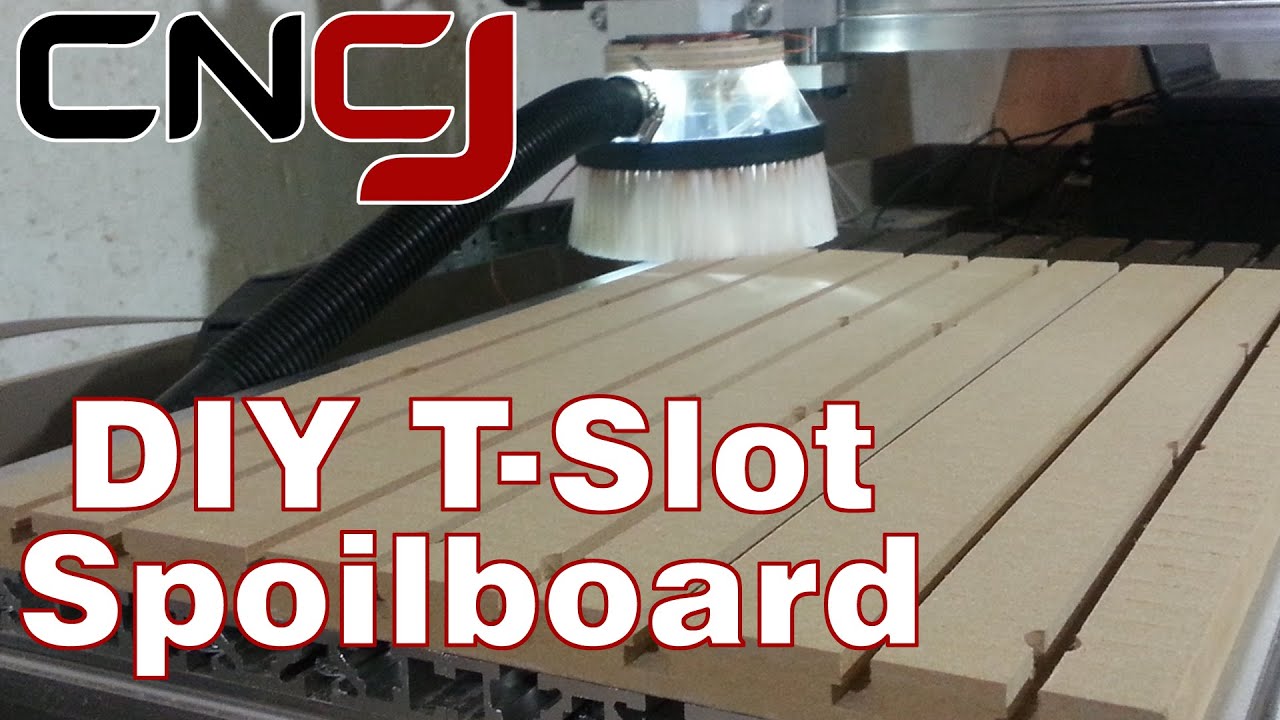
To cut the biscuit slots for the shelf, draw a pencil line across the inside face of the side and clamp the edge of the shelf against the line. Next, mark your biscuit slot marks on the top of the shelf. Resting the biscuit joiner on its base, place it on the side and cut the slot for the shelf as in Photo C. The base also serves as your reference when slotting the sides. Turn the joiner on its head, use the line engraved on the bottom of the tool to align it with your slot marks, and plunge it into the side, Photo D. Once cut, insert biscuits into the grooves and flip the shelf up on the location line.
Stick the board’s end over the edge of your bench so that the fence, not the tool’s base, sets the slot depth.
Balance the biscuit joiner’s fence on the end of the side panel to cut the grooves in the face.
Face-to-edge joints are the bread-and-butter joint for biscuit joiners. A biscuit joiner can cut the needed joints to assemble a cabinet in about as much time as it takes to drag a heavy sheet of MDF to your table saw.
Building a simple box provides a good opportunity to explore the advantages and disadvantages of fence- or base-guided slot cutting. Sometimes, you’ll have the freedom to choose the method, but sometimes the decision is made for you. Box-making uses both.
First, position the side and end panels together and draw lines across the joint to mark where you want a biscuit. (As a rule of thumb, place the biscuits about 6' apart.) When you pull the panels apart, you should see marks on the edges and ends.
To cut the grooves in the edge of the end panel, place the work flat on the workbench, as shown in Photo A. Adjust the fence so that the blade cuts a slot roughly through the center of your work. To cut the face grooves in the side, you’ll balance the fence on the panel’s edge as shown in Photo B.
Remove or retract the fence and use the joiner’s base to cut the slots in the end of the shelf.
Don’t move your wood; just flip your joiner so that the base rides against the shelf. Plunge the joiner into the side.
Biscuit Sizes
To cut grooves for most of the biscuit sizes (0, 10, 20), simply adjust the stop on your biscuit joiner. Smaller FF (or face frame) biscuits are available for the Porter-Cable biscuit joiner. To use these mini biscuits, you’ll need to switch out the standard 4' dia. cutter with a smaller 2' dia. blade.
THE END-TO-EDGE AND MITERED BISCUIT JOINTS
Biscuits are also an easy way to build mitered and end-to-edge frames that you would use for picture frames or for a cabinet’s face frame. In this case, biscuits are very useful because they are adding reinforcement to otherwise weak end-grain joints.
Start by selecting the right biscuit. An easy way to do this is to position the joint together then arrange one or more biscuits on top. Drawing a center line on a test biscuit can help you lay out the slots as shown in Photo E. Wider biscuits provide more strength (even if you saw off an end), but there are times when you want the biscuit to be hidden within the joint. When form is as important as function, use the Biscuit Sizing Chart on page 13. When picking a biscuit, don’t forget the wiggle room. The slot is usually about 3/16' wider than the biscuit you’re trying to fit.
Cutting Slots In Composite Decking
When slotting narrow pieces, don’t hand-hold the stock. Because a portion of the blade will be exposed while making the cut, and since the spinning blade can “walk” if the tool or work isn’t properly held in place, it’s too easy to get hurt. Eliminating the risk of a visit to the ER is easy: simply clamp narrow pieces to a stopblock as shown in Photo F.
You can now align the center mark on the joiner with the marks on your stock and make the cut. After making the cuts, glue the biscuits into their slots and clamp the frame together. Once the glue has dried, you can slice off the protruding biscuit tip as in Photo G.
Position the bigger biscuit so that it won’t protrude into the visible inside edge of the frame.
Use clamps and extra backup, not your free hand, when cutting narrow stock.
Cutting Slots In Mdf Boards
Saw off the biscuit tip with a handsaw or using your table saw and crosscut sled.
Double-Biscuit Joinery
Biscuits don’t fare well when matched against other joints in wood-joint torture tests. Because biscuits are relatively short, it doesn’t take a rocket scientist to realize that this joint isn’t as strong as traditional mortise-and-tenon or half-lap joints.
Cutting Slots In Mdf Sheets
An easy way to strengthen a biscuit joint is to cut two grooves, as shown at right. In seconds, you’ve doubled the gluing area of the joint. Try to leave a ¼'- to ½'-strip of wood between the biscuits to maximize available gluing surfaces and preserve the strength of the wood. (With careful spacing, you can use the double-biscuit technique on a ¾'-thick rail and stile joint.)
To cut the grooves, I prefer to use spacers instead of my fence. Referencing the joiner and working against my bench is fast, and for those times when I forget to cut a slot, easily repeatable.
face miters
Cutting Slots In Mdf Board
Face miters are A way to hide end-and edge-grain when making solid wood boxes or plywood cabinets, but long miters are tough to glue and tricky to reinforce. A few biscuits can solve both problems. They can register the ends so that the corners can’t slip during clamp-up and strengthen the otherwise end-grain joint. A biscuit-reinforced miter is as strong as a full table saw-cut spline, but biscuits can be hidden within the miter for a cleaner-looking joint. (With the table saw, you cut the spline from edge to edge.)
To cut a slot in an angled edge, use your fence. How you cut the slots in the mitered face depends on the fence-adjustment flexibility of your biscuit joiner and your working style. If your router has a fixed fence (or if you prefer working with your workpiece flat against your bench) you will want to try making your cuts as shown in Photo H. Set your fence to 45°, adjust the cutter depth so that it doesn’t slice through the thinner tip of your miter, and make a plunge cut into the end.
Some joiners, like the Porter-Cable 557 (see the Buying Guide) have a two-stage fence that can reference the outer face of the miter as shown in Photo I. This design prevents corner alignment problems, especially if the stock thicknesses aren’t equal. The wrap-around style of this fence also makes it easier to hold the tool in place while making the cut.
Adjust the fence height or add a shim so that the blade does not cut through the tip of the miter.
When the fence is set to 135°, you can squeeze the joiner against the miter as you cut the biscuit slot.
offset joinery
There are times, as when joining a rail to a leg where you may not want a flush-fitting joint. Your biscuit joinser is equally adept at creating offsets. The trick is to use a spacer that the same thickness as your desired step back. The spacer-offset trick can be used with your biscuit joiner’s fence, or under the base of the tool, as shown here. (I think resting the joiner on top of a large hardboard spacer is alot easier than trying to sandwich the spacer between the work and biscuit joiner’s fence.)
To make the offset joint, mark the leg and apron for the biscuit slot just as before. Now choose a spacer that is the same thickness as your desired offset.
Position the spacer under the jointer as shown in Photo J, position the leg with the show face against the bench and cut the slot. To cut the matching slot in the apron, simply remove the spacer and slot the end of the board as shown in Photo K. Be sure the show face is touching the bench.
THE EDGE-TO-EDGE BISCUIT JOINT
You might want to think twice before using biscuits for solid-wood edge joints (See “Biscuits or No Biscuits?”). but biscuits are very useful for attaching solid wood edging to sheet goods, and also when you need to straighten out bowed boards. With practice, you may be able to biscuit an edge joint in less time than it takes to read how it’s done.
To start, position the boards edge-to-edge, then make short pencil lines across the joints about every 8' for the slots, as shown in Photo L. Make the first and last slots at least 3' in from the end; that way, you won’t accidentally expose a biscuit if you trim the panel later.
Next, set the joiner’s fence height to cut a slot roughly in the center of the board. To ensure that the joiner’s fence is setting the slot height, and not the base, clamp the board so that the edge sticks off your bench as shown in Photo M. Let the cutter reach full speed before plunging it into the wood.
You’re now ready for glue-up. Because the biscuits swell quickly, do a dry assembly and make sure everything’s set before you open the glue bottle (Photo N). Remove any sawdust from the slots, test-fit your biscuits, and dry-assemble the panel. If everything fits like it should, you’re set to reassemble it for good with glue.
Keep the fence flat on the board surface when cutting slots.

Use a biscuit-slot bottle to quickly squeeze glue into the slots.